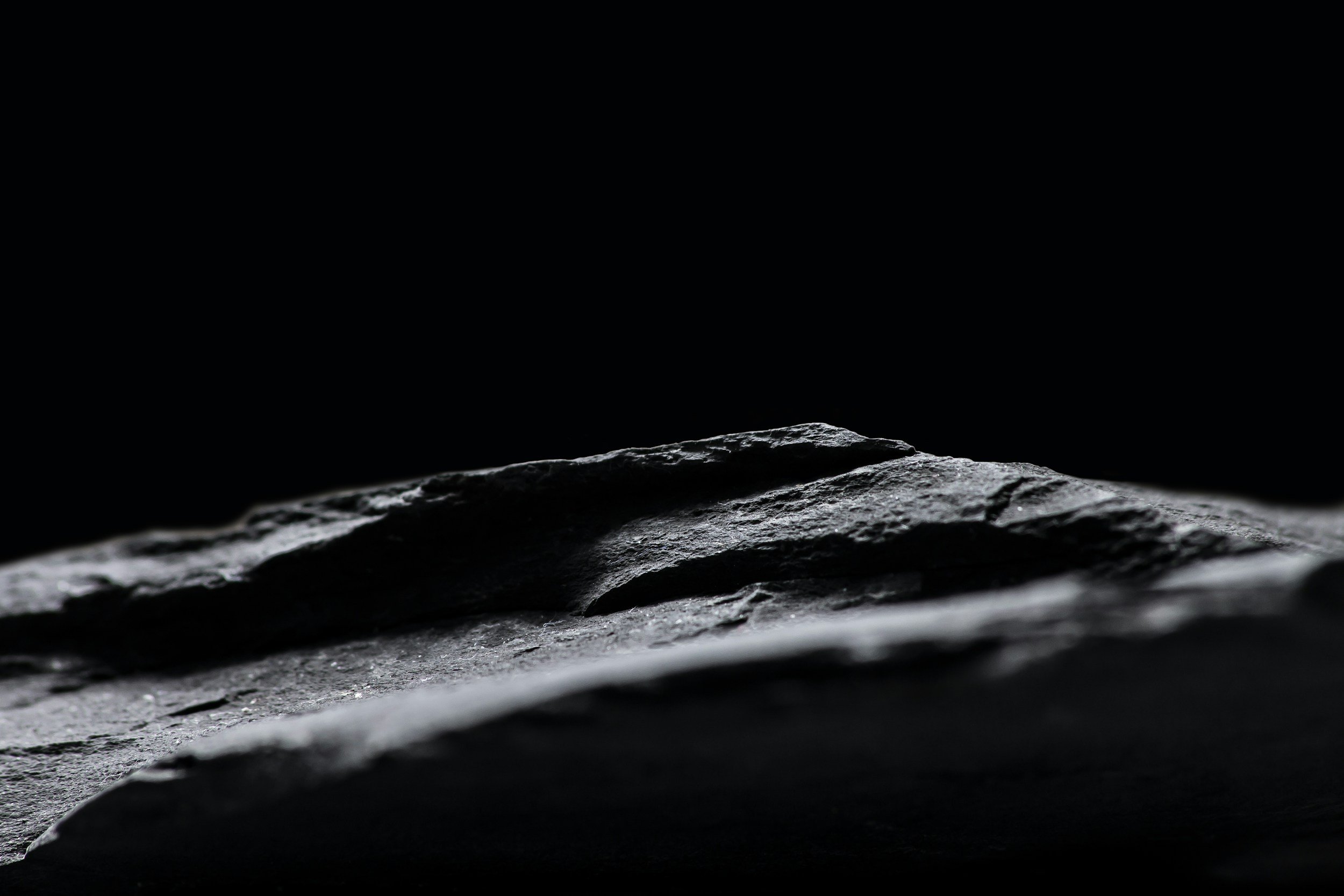
Ghost Solutions LLC
Enhanced Solutions Tailored to Your Engineering Needs
Delivering personalized engineering consulting expertise, backed by decades of hands-on experience and innovative solutions.
Our approach
Our specialized approach to engineering consulting is designed to meet your unique needs and requirements. Ensuring optimal solutions tailored specifically for each project. With over a century of combined engineering experience, our mission is to create a customized plan that delivers the best results. We take pride in our commitment to excellence and go the extra mile to exceed client expectations. As trusted engineering consultants, we foster positive partnerships and continuously strive for meaningful, high-impact outcomes. Contact us today for an initial consultation and discover how we can tailor our services to suit your specific needs.
World-class engineering consulting
Why Choose Ghost Solutions?
Tailored Strategies: We listen closely to your needs and design solutions that are as unique as your challenges.
Expertise You Can Trust: Our deep industry knowledge and data-driven insights ensure that we always find the most effective path forward.
A Commitment to Excellence: We go the extra mile to not only meet but exceed your expectations.
Long-Term Partnerships: We believe in building strong, positive relationships with our clients that foster continued success.
Let us show you how Ghost Solutions can unlock the full potential of your projects. Contact us today for an initial consultation, and let’s explore how we can create the ideal solution for your needs.
In-person and remote options
Headquarters in Rock Springs, Wyoming: Serving Global Engineering Consulting Needs
At our Rock Springs-based headquarters, we are proud to serve not just the local community but also a global platform for all your engineering consulting needs. Specializing in Soda Ash, Lithium, and various other mining and extraction processes, our expertise ensures that you receive the highest level of insight and support for refining and optimizing your operations.
Ready to take your project to the next level? Call us today to set up a consultation.
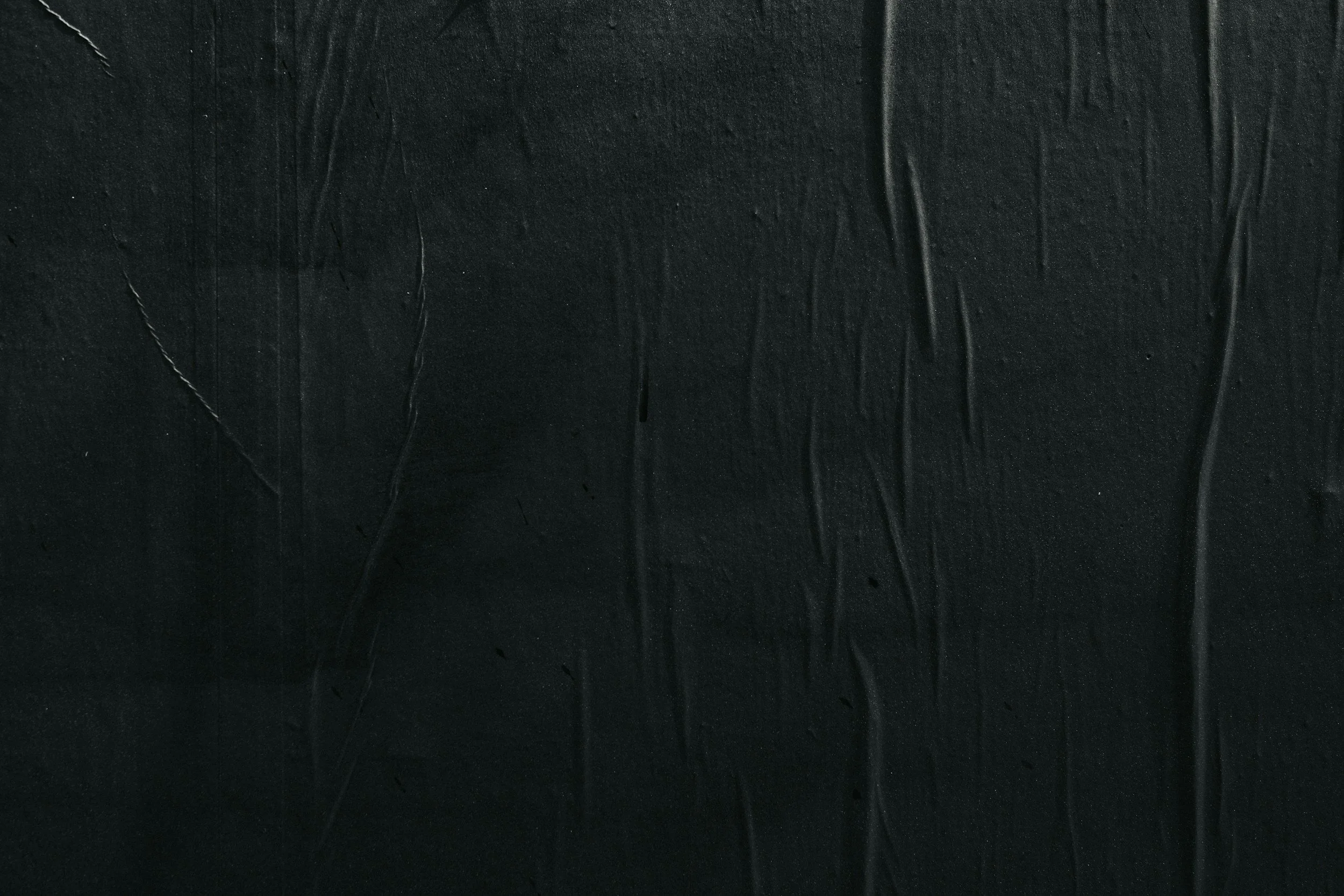
Our services
-
Engineering Analysis
-
Specialized Consulting
-
Process Modeling
-
Data System Development & Integration
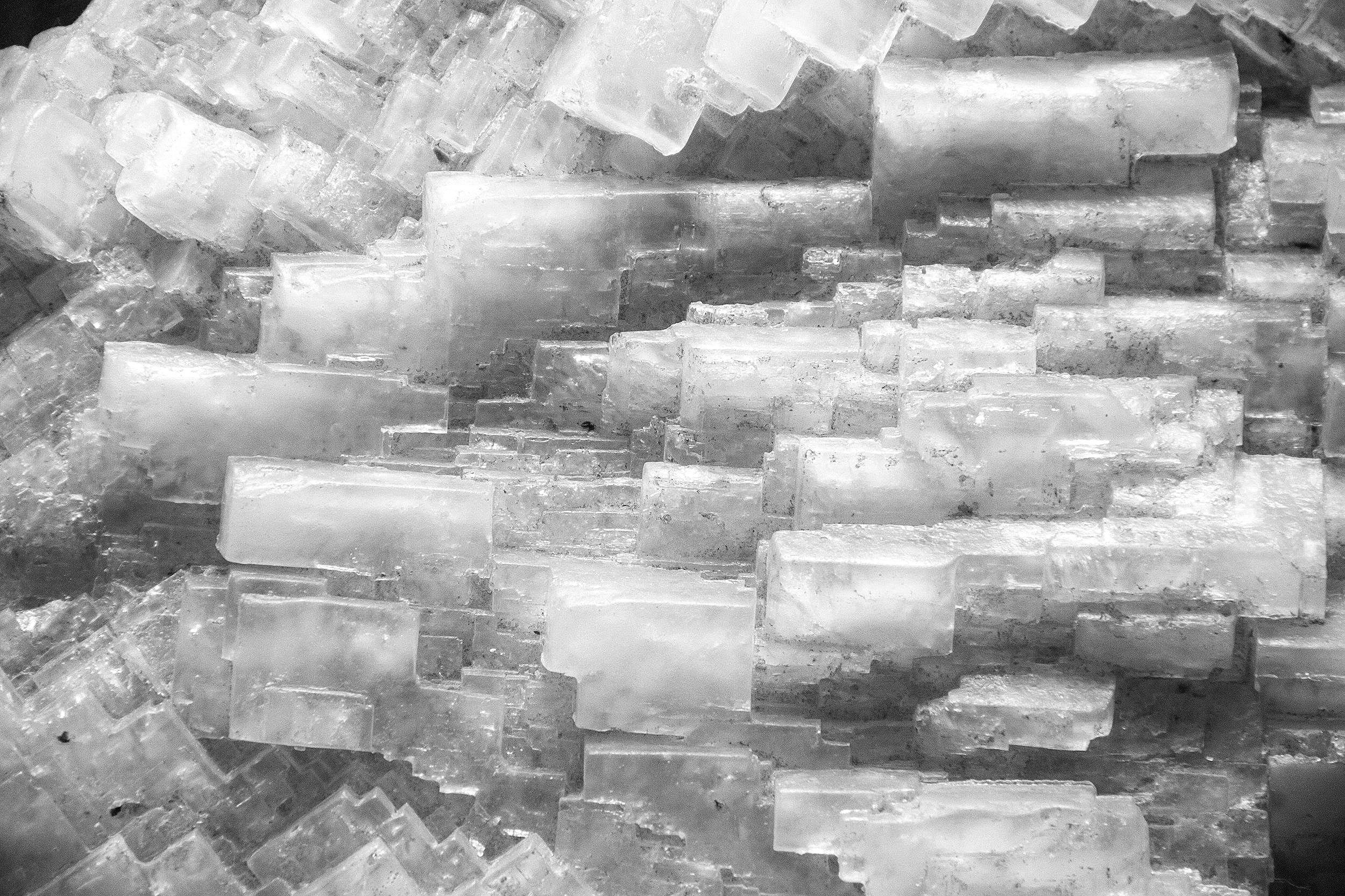
“Innovating the future to meet the
highest of demands .”
Highlights
Industry Leaders
Influential Women in Manufacturing
Featured Presenters
Community Involvement
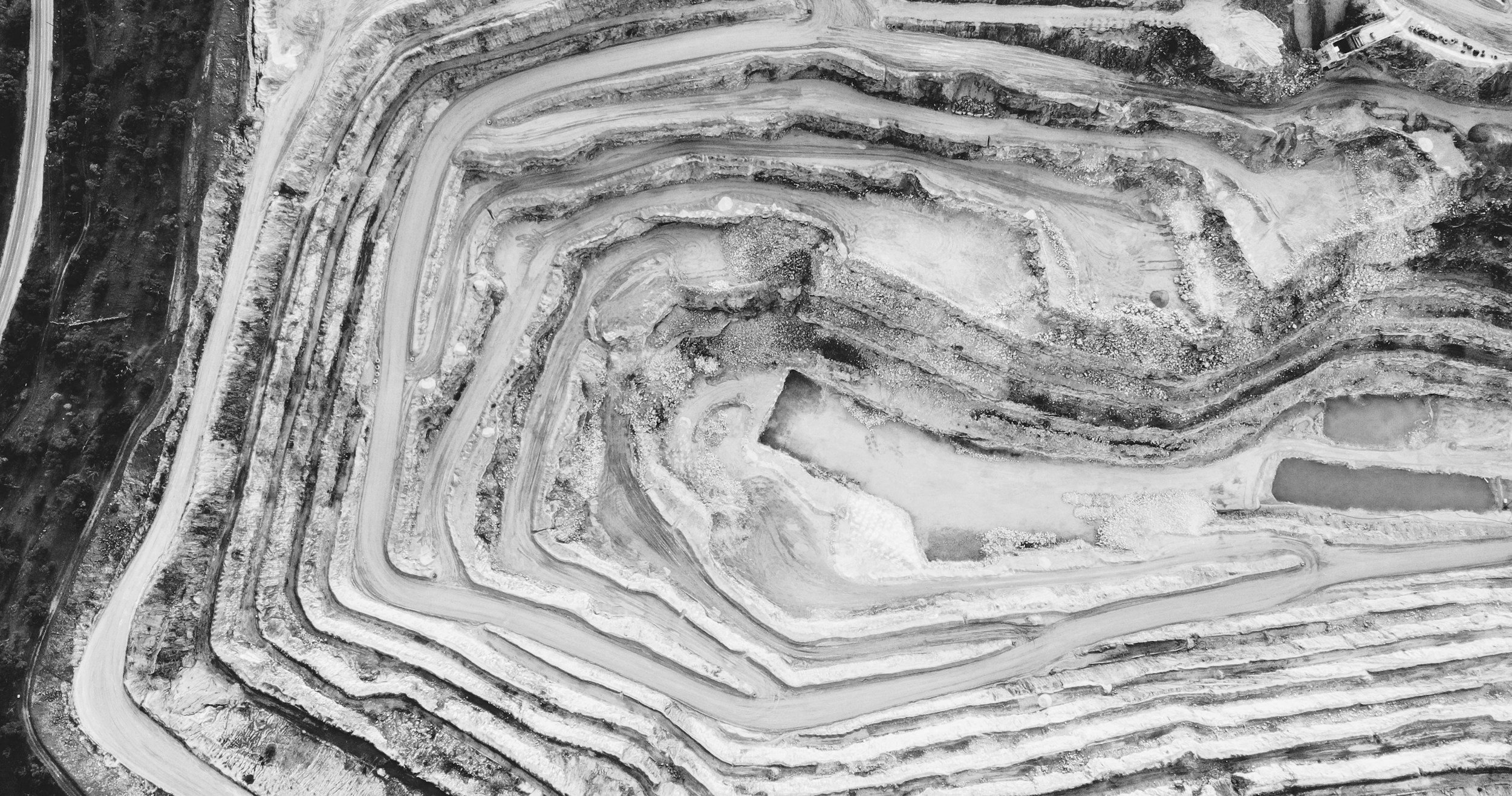
Ghost Solutions LLC